-
No. 34 Xiayaopo, Bopu, Wuchuan City
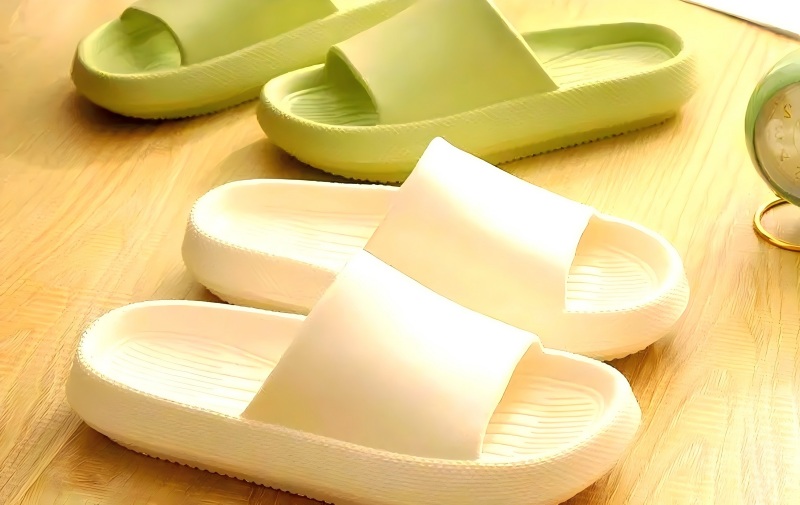
Mastering EVA Shoe Standards: Boost Comfort in 6 Steps
Abstract:
EVA shoe materials have become the core materials of the modern footwear industry with their light weight, flexibility, wear resistance and other characteristics. Its excellent performance and comfort are derived from the strict compliance with the six core standards of density ratio, thickness design, appearance control, performance testing, environmental protection upgrade and authoritative certification. A deep understanding of these standards is the key for consumers to choose high-quality shoes and manufacturers to improve their competitiveness.
1. Core density: the performance division between soles and insoles
EVA shoe materials are not a single formula. The soles need high density (usually >0.20g/cm³) to provide rigid support and impact resistance to ensure walking stability (refer to ASTM D792 density test standard). Insoles rely on low density (usually <0.15g/cm³) to achieve lightness, softness and rebound cushioning. For example, professional running shoe insoles can effectively absorb up to 70% of impact energy (based on sports biomechanics research). Wrong density selection will cause the sole to collapse easily or the insole to be too hard and lose elasticity.
2. Scientific thickness: precise adaptation of functional requirements
Standards are by no means one-size-fits-all. Sports shoe soles need to be thick enough (usually 8-15mm) to ensure cushioning, and the thickness of the midsole of basketball shoes even affects the safety of athletes landing (NBA sports medicine report points out the correlation between foot injuries and midsole thickness). The thickness of the insole (mostly 3-8mm) needs to match the space of the shoe cavity. Too thick squeezes the foot, too thin loses support, and customized insoles need to accurately scan the arch shape (with the help of CAD/CAM digital design).
3. Flawless appearance: the first line of defense for quality reputation
Minor defects indicate potential failure. The standard strictly requires no bubbles, impurities, obvious color difference or deformation on the surface of the sole/pad. A tiny bubble may expand into a fracture source after repeated bending (simulation tests show that the stress concentration factor at the defect is as high as 3 times); color difference directly damages the brand image. Well-known brands’ production lines are equipped with high-speed visual inspection systems (such as Keyence optical solutions) to remove defective products in real time.
4. The iron law of performance: laboratory data verifies the durability limit
Paper standards need to be tested in practice. Bending resistance test (such as GB/T 20991 50,000 bending simulation) ensures that the soles do not crack in winter; Abrasion resistance (Taber or DIN abrasion tester) determines the life of the soles, and qualified EVA has a 40% higher wear resistance than ordinary rubber; Impact resistance (drop hammer impact test ASTM D5420) verifies the safety protection value. The international testing agency SGS report shows that the life of qualified EVA soles can exceed that of ordinary materials by 2 years.
5. Environmental protection upgrade: green responsibility throughout the life cycle
From raw materials to waste, everything needs to be sustainable. Leading standards require limiting plasticizers such as phthalates (in compliance with EU REACH Annex XVII), using solvent-free water-based foaming technology to reduce VOC emissions (60% reduction compared to traditional processes), and exploring bio-based EVA and degradable formulas (such as DuPont’s latest plant-based EVA material). The demand for shoes certified by the global recycling standard GRS has increased by 35% annually (Textile Exchange data).
6. Certification authority: a global passport of trust
Third-party endorsement dispels market fog. SATRA technical certification (the world’s top footwear research institution) is the golden mark of excellent performance; ISO 9001 quality management system ensures production consistency; OEKO-TEX® Standard 100 certification eliminates harmful substances. EVA insoles certified by SATRA PM144 have significantly optimized the uniformity of foot pressure distribution (biomechanical testing improves comfort by 18%).
Summary:
EVA shoe material standards are not just cold rules, but a sophisticated system that integrates material science, ergonomics and environmental responsibility. From the precise ratio of density and thickness to the flawless control of appearance; from the rigorous performance verification in the laboratory to the environmental protection upgrade and authoritative certification throughout – the six dimensions together build the cornerstone of comfort and durability underfoot. For consumers, this is a navigation map for selecting high-quality shoes; for the industry, this is the core engine for moving towards high-end and sustainable development. Only by deeply understanding and abiding by these standards can we move forward steadily in the global competition of the footwear industry.