-
No. 34 Xiayaopo, Bopu, Wuchuan City
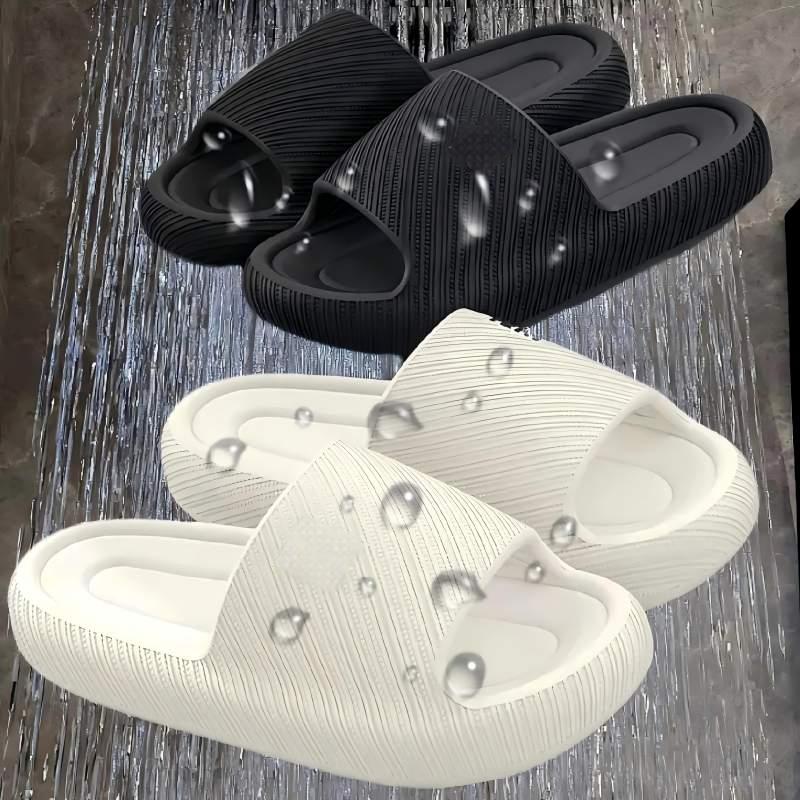
EVA Slippers Crafting: Advanced 6-Stage Factory Process
In the fast-paced modern life, a pair of light, comfortable and durable EVA slippers has become a daily necessity for hundreds of millions of families around the world. Market research shows that the global EVA slipper market is expanding at an annual compound growth rate of 8.2% (Grand View Research, 2023). Behind this seemingly simple foot enjoyment, there is actually a series of sophisticated and complex process innovations. This article will deeply analyze the six core processes of EVA slipper manufacturing and reveal how technology transforms basic materials into works of art on the tip of the foot.
1. Hot pressing: a mechanical revolution of molecular cross-linking
The transformation of EVA (ethylene-vinyl acetate copolymer) raw materials began with hot pressing. When precisely cut EVA particles are subjected to 160-180℃ high temperature and 15-20MPa high pressure (Journal of Polymer Engineering and Science), their molecular chains undergo cross-linking and reorganization. This process is like precision forging in the microscopic world, which not only shapes a three-dimensional sole structure that conforms to ergonomics, but also gives the material excellent rebound performance and energy absorption capacity. The difference in temperature and pressure directly determines whether the finished product is soft as cotton or tough as armor.
2. Precision cutting: the art of boundary with millimeter-level error
The hot-pressed sole needs to be cut with high precision to give it the final shape. Modern laser cutting technology can achieve a processing accuracy of ±0.1mm (Industrial Laser Solutions report), making complex designs such as V-shaped water guide grooves and Y-shaped support skeletons leap from drawings to reality. This micron-level precision separation not only achieves the visual aesthetics of the product, but also optimizes the drainage and anti-skid function – research has confirmed that properly designed grooves can increase the friction of wet roads by 40% (“Footwear Technology” journal).
3. Bonding revolution: chemical welding beyond physics
The combination of upper and sole is the essence of craftsmanship. When the environmentally friendly polyurethane hot melt adhesive is precisely applied at 120℃ (Adhesives Age Technology White Paper), it will penetrate and fuse with EVA at the molecular level. The strength of this chemical bond can reach 3 times that of traditional glue, ensuring that it will not come apart even after repeated bending 100,000 times when worn. The advanced fully automatic dispensing robot uses a visual positioning system to control the glue line width error within 0.3mm, achieving the aesthetic effect of “invisible welding”.
4. Micro-carving modification: the ingenuity of the universe in the details
In the micro-modification link, the high-speed CNC machine tool mills the edge with a precision of 20,000 rpm (Modern Machine Shop data) to eliminate all burrs and flash. Surface treatment technologies such as micro-sandblasting and plasma activation can increase the surface energy of the material by 5 times (“Surface Engineering” research), providing a perfect canvas for subsequent printing and hot stamping. A leading brand uses nano-imprinting technology to replicate the micron-level texture of rose petals on the upper, sublimating practical products into works of art.
5. Extreme quality inspection: data-driven quality wall
Each pair of slippers must pass strict quality inspection:
- 3D scanner compares the real object with the design model at a resolution of 0.02mm
- Wear test machine simulates two-year wear loss at 5200 rpm (SATRA TM31 standard)
- Color difference detector protects visual uniformity in the ΔE<1.0 range For factories certified by ISO 9001, the defect rate must be controlled below 0.3%, so that each pair of shoes can stand the test of time.
6. Green packaging: Sustainable end declaration
Terminal packaging is undergoing an environmental revolution. Frontier companies use corn starch-based bioplastics to replace traditional PE film, and its 180-day natural degradation rate exceeds 90% (European Bioplastics data). Through topological optimization, intelligent packaging design can increase the utilization rate of transportation space by 35% and reduce carbon emissions by 22% (“Sustainable Packaging Solutions” case library), allowing comfortable footprints to extend to the earth’s ecology.
From molecular reconstruction during hot pressing to carbon footprint control in the packaging process, the manufacture of EVA slippers is actually a symphony of material science, precision machinery and sustainable development concepts. When global industry giants have invested in the research and development of EVA foaming closed-cell rate improvement technology (the current cutting-edge level is 95%) and recyclable EVA closed-loop production system, we see not only the evolution of foot comfort, but also the future picture of human beings weaving with technology and reconciling with nature. This pair of seemingly ordinary slippers is taking a solid step towards green manufacturing.
Authoritative reference sources: [1] EVA material properties: https://www.omnexus.specialchem.com/polymer-properties/properties/ethylene-vinyl-acetate [2] Laser cutting accuracy: https://www.industrial-lasers.com/cutting [3] Hot melt adhesive technology: https://www.adhesives.org/adhesive-technologies [4] Biodegradable plastics: https://www.european-bioplastics.org/ [5] SATRA testing standards: https://www.satra.com/standards/testing_methods.php